BILCO DOOR FOR NEWARK HOUSE
By Eric Martindale Feb 5, 2024
THOUSANDS OF HOUSES NEED A NEW CELLAR DOOR
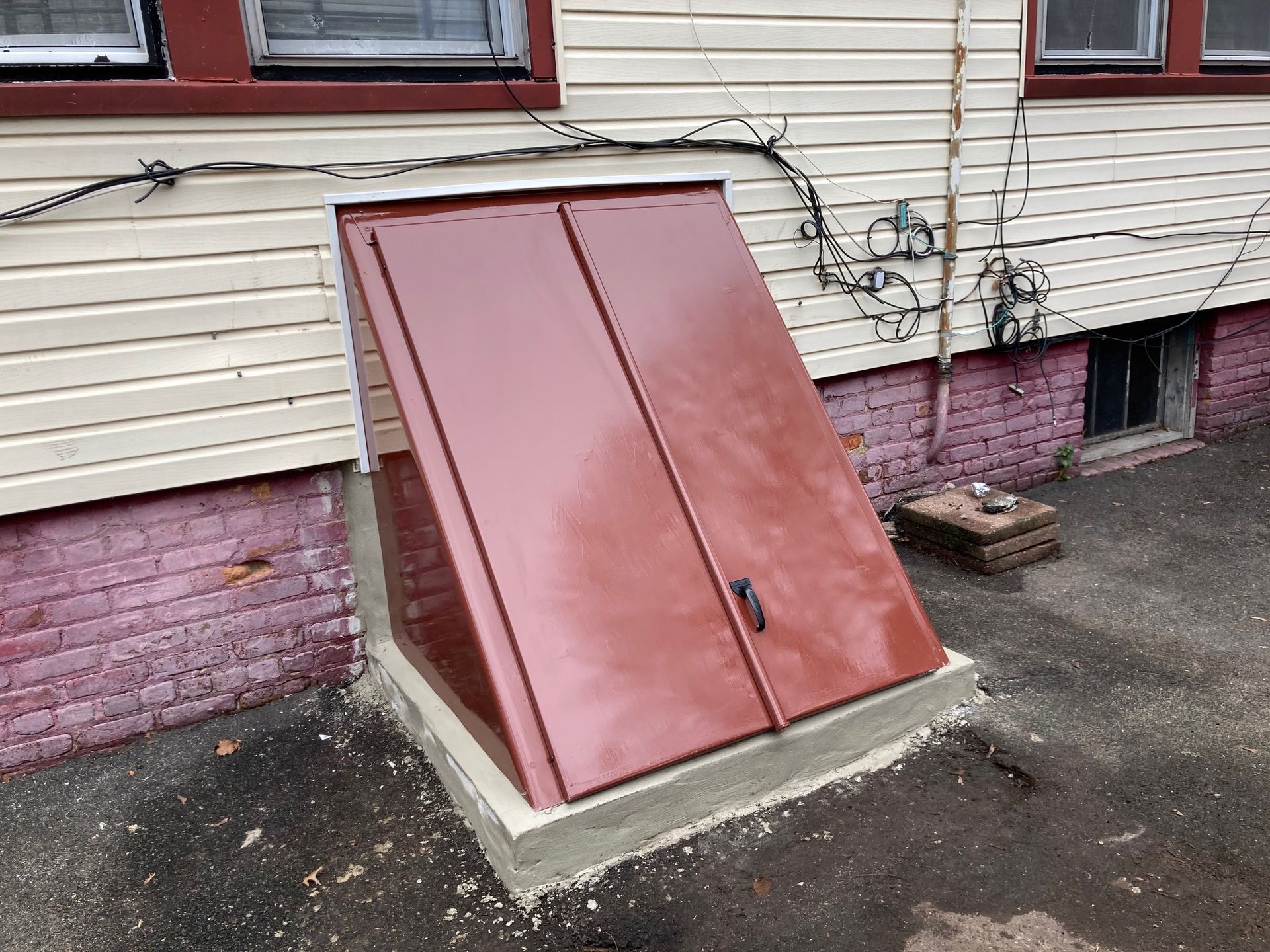
When it’s time to fix up the house, it’s often best to start with the foundation, and work your way up. A young lady in the Weequahic Section (aka “The Mighty South”) of Newark called us in January, hoping to add a Bilco door to secure her home, and have a workable entrance for contractors to finish the basement. Confident Home Remodelers is New Jersey’s leading installer of cellar doors, also known as Bilco doors or Steelway doors.
She’s living on one floor, and has family members renting the other floor at a discounted rate. It’s nice to see people providing for family members in need of affordable rental housing. We respect that.
We’re used to showing up at an appointment and seeing a tarp over a leaking cellar door. Not this time. There was nothing there but old rotten plywood. “Don’t step on it”, she said “It will collapse and you’ll fall into the stairwell”. That was the heaviest piece of plywood I’ve ever had the pleasure of moving. The water really adds to the weight of the board. Sadly, the opening wasn’t any much better after we removed the plywood.
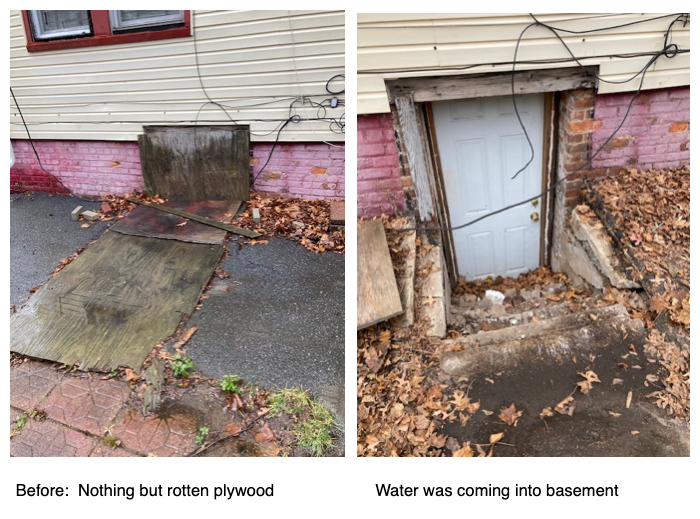
The foundation and the stairs were severely crumbling. The house was over 100 years old, and this was the original masonry, without any repairs in all those years.
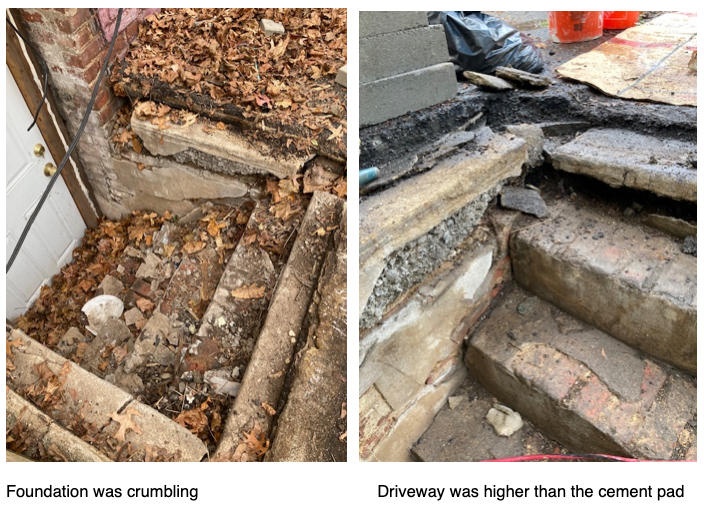
We sold the deal, and due to the shape of the foundation, the only unit that would fit was the large Bilco SL series. The customer decided to go with “Rustic Red” as the glazing color, to match the trim around the windows. See below picture of the house. The house is better than average for the neighborhood, and has large rooms throughout.
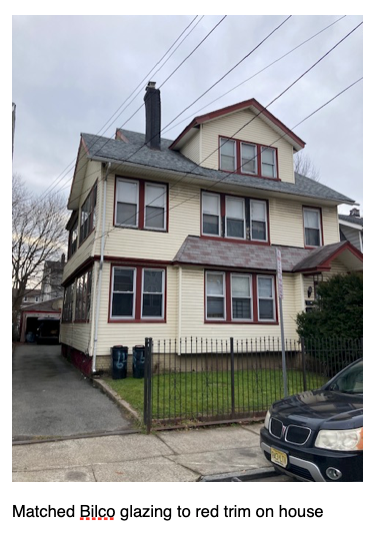
This shade of red trim is quite popular in the urban areas. It’s a deeper red than the red primer on a Bilco. We glazed both sides, every square inch, prior to delivery. We buy the glazing chemicals from a glazing supplier. The glazing is non-porous on the molecular level, blocking out all rust. We do not “paint” our cellar doors. Glazing costs more than paint, but we’ve never had an owner-occupied homeowner say, “I want to save the $200 difference, you can paint the Bilco instead of glazing it.” We’ve solved the rust problem with these cellar doors, and that’s why people are signing our contracts.
In consultation with the customer, we decided that the best approach was to remove some of the asphalt covering the collapsing foundation, level it, and raise it just a bit so that water will not come in. Flat properties with driveways tend to develop water problems with their Bilco’s, because when the driveway is repaved, suddenly parts of the Bilco are below grade.
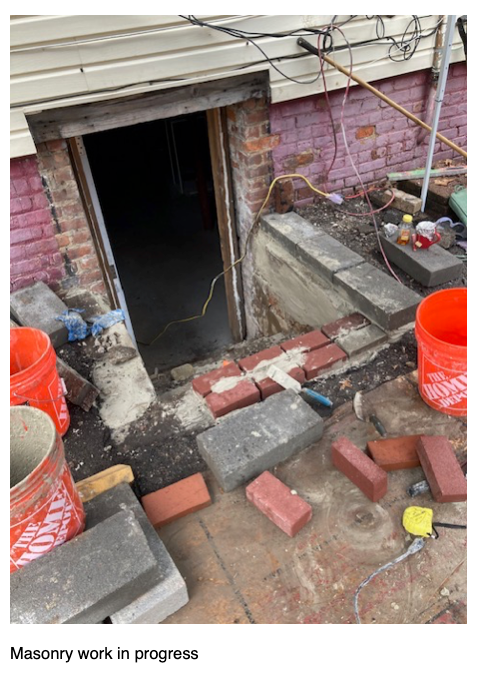
After the excess asphalt was removed, we determined that the back right corner was 2 inches higher than the front right corner, and almost 3 inches higher than the front left corner. Well, that’s on me. I saw the opening, and it wasn’t fully covered with asphalt. We knew it wasn’t level. I gave the price, and levelling it was part of the contract. Probably I would have asked a tad more if I knew what was involved, but we got the job done. If during the demolition, I find something completely out of sight, such as a buried electrical or plumbing line, or a termite-infested sill, that’s a valid reason to tell the customer there’s going to be a cost addendum. If I say we’ll level a unit, and the levelling is more work than I thought, that’s just on me.
We jackhammered about an inch off the highest parts of the right foundation side, and we added an assortment of standard bricks and extra-thin bricks along the front. We then laid a level of 4” solid cinderblocks, and we leveled and squared everything while the cement was wet. The weather was on the cold side for cement work, a bit below the magic 45 degrees. The key is that it was not below freezing overnight, or the prior day. If there had been a frost or freeze overnight, we would not have installed that day, because the masonry really “holds” the freeze all day. We know quite a few masonry tricks, and we used one of them to make sure that our hydraulic anchor cement would set fast in such cool weather. It was hard in one hour.
Also, take note that even low 50’s temperature would have been no good for masonry work if had been 25 degrees overnight, and then dipping that low a few hours after the work. The 45-degree masonry rule has some serious footnotes.
I don’t want to make it look easy, because it was not. We used our tools to ensure that the new foundation was exactly perpendicular to the wall, square on all corners, level horizontally, and in this case projecting 45” from the house wall on both sides. There’s an order to installing the new cinderblocks, and they don’t go in consecutive. That’s another trade secret. You have to know where to start, and the pattern of laying down the cinderblocks. Any good mason reading this knows what I’m talking about. Anyone not understanding should not attempt to rebuild a cellar door foundation.
Here’s the new foundation completed. We put the old plywood back, and called it a day. My fingers were getting numb.
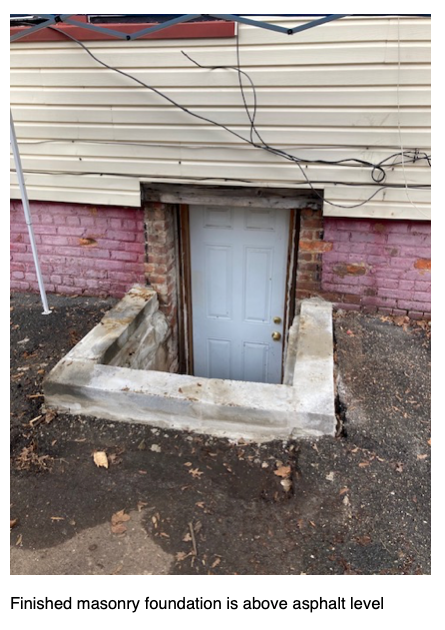
A week later there was another day warm enough to work, and not raining. We returned to do the main install. I secured pressure-treated 2x4’s to the bricks, using a masonry gun, extending down from the sill to the foundation. On this particular install, there was a 1.5” gap between the house foundation bricks and the unit due to the positioning of the house sill plate, so we had to fill that gap. We later buried these 2x4’s in our special cement. We don’t leave exposed wood on our installs.
In preparation to secure the Bilco, we carefully cut and removed a section of vinyl siding and ½” Styrofoam insulation. You can’t cut the opening the same size as the Bilco, because that makes it problematic to secure the new J-channels. They’ll either be too tight, or there’s too much gap. Additionally, the top flange has to slip under the existing siding. It can’t be cut too high or it will look silly, and it can’t be too tight or the screws to attach the J-channel will be hitting the metal top rail. There’s a sweet spot, and there’s no more than ¼” tolerance up or down. It was trial-and-error for quite some time, on different job sites, to figure this out. Is it best to install the J-channels first, or the Bilco first? Ah, ah, ah, my competitors might be reading this article. Yes, there’s an order to these steps, and it’s not readily apparent. We’re not revealing this valuable information.
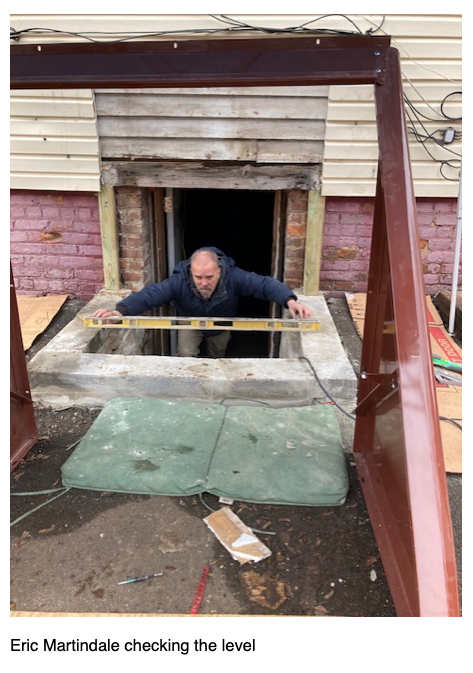
During the install, we decided to take pictures of what we consider to be a design flaw with the Bilco SL unit. We’ve been cursing the SL unit for years, every time we install one. The last pre-drilled hole on the rear of the triangular foundation is not easy to secure, either with a screw or the Bilco nail-pin. The angled cross-bar support is in the way. See the angle I have to hold the drill, in the below left picture. It’s very awkward. Of course, we’d prefer it to be perpendicular. It we were securing the Bilco to the foundation directly, that’s the awkward angle for the Bilco nail-pin as well. The right picture below shows a finger pointing to where we think the hole should be. I am going to send this information to Bilco, and ask them to slightly change the SL design.
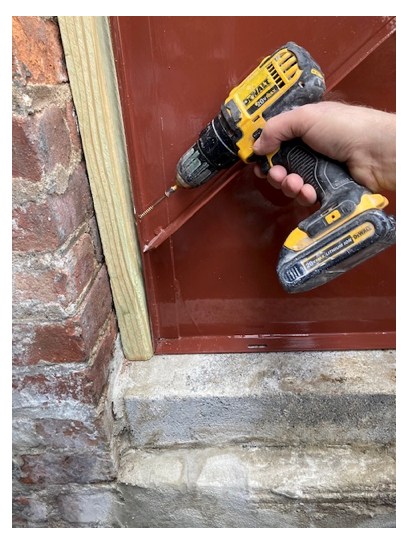
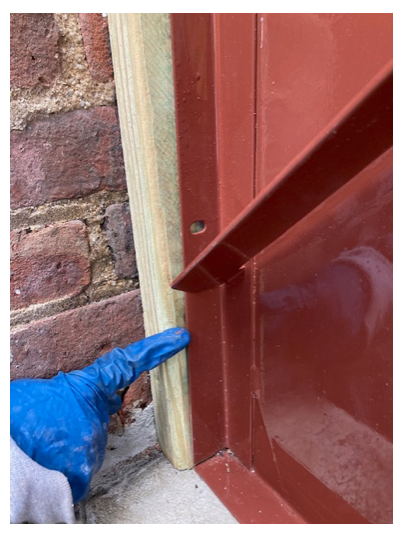
Design flaw on Bilco SL. We'd prefer the drill hole to be here.
Almost ready for the post-install cement. That’s the original wood clapboards of the house, exposed for the first time in decades. Almost every house in Newark once looked like that, most with peeling lead paint and exposed rotten clapboard corners. It’s interesting that this house was never painted, and later the vinyl siding was added.
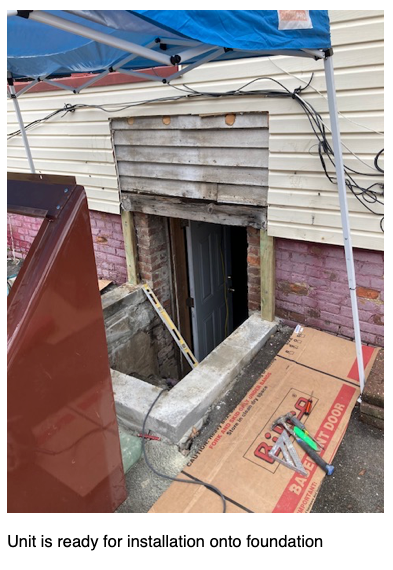
We sloped our hydraulic anchor cement up against all metal edges and flanges inside and out. The hydraulic quality keeps water from soaking into the cement, and the anchor quality prevents it from cracking away from the metal, and allowing condensation or rainfall to get into the gap and rust out the unit. Do not ever use Type-S mortar to install a metal cellar door. That’s a guaranteed failed installation. The Material Data Sheet for Type-S Mortar says it’s for masonry contact only, brick to brick, or cinderblock to cinderblock. It is specifically written that Type-S Mortar is not for steel contact. Better listen to what they say.
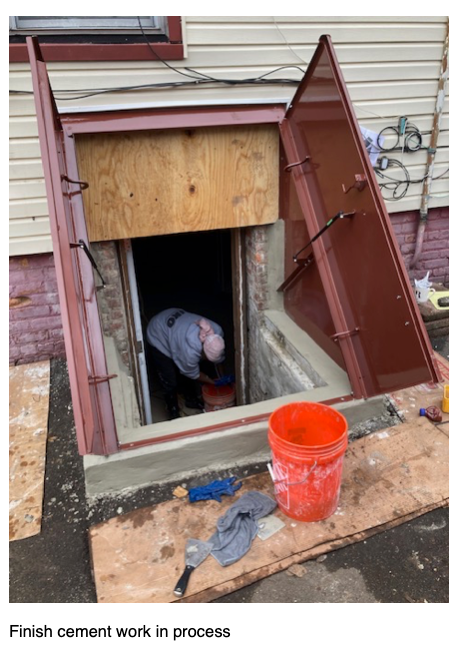
Done and beautiful. We skim-coated the exterior foundation. Notice also that we angled some cement to cover the vertical pressure-treated 2x4. The customer had a spare piece of plywood stored in the garage. We offered to cover the ugly old wooden clapboards, a no-charge freebee. She can paint it in her spare time. Below is the finished install. Now that there is a good cellar entrance for workers to come and go, the customer can get the basement finished.
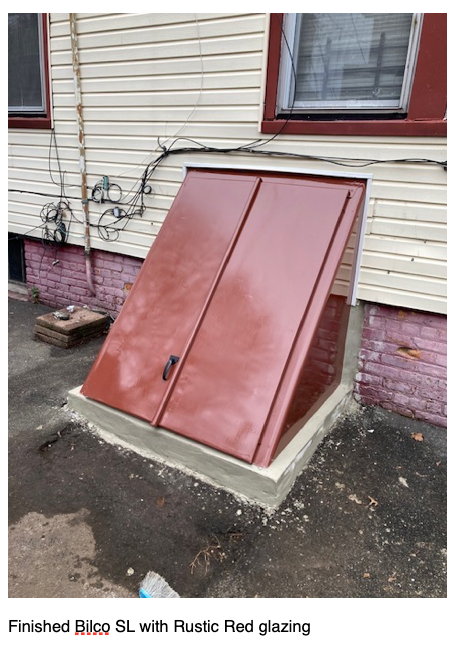
The customer’s rear yard is quite small, and it’s half-paved, half-grass. When the job was done, the customer remarked that she really likes the tall SL-Bilco unit, because the traditional units project out further, and that would take away from usable space for outside family gatherings. They’ll all be coming in the Spring and Summer, and will be quite impressed to see the new Bilco. If I’m lucky, I’ll get some referral business.
Here’s a side view
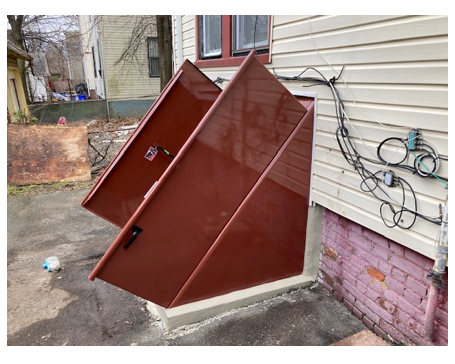
We take great pride in our work. All customers deserve to have quality work done on their homes, whether it’s an old house in a working-class urban neighborhood, or it’s a multi-million-dollar estate. We do them all.
For more information, and to review all of our blog postings, see www.glazedcellardoors.com We install cellar doors throughout Central and Northern New Jersey, and Eastern Pennsylvania.